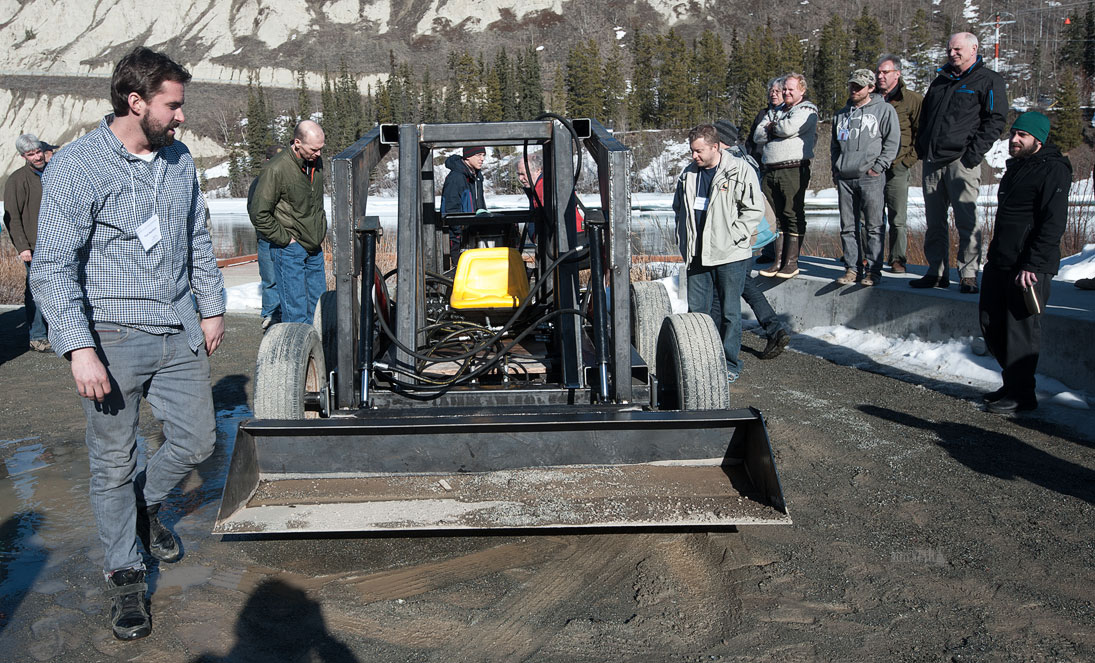
Photo by Vince Fedoroff
TILLING SUCCESS – Tom Bamford (far left) is seen Tuesday with the home-built tractor. It is headed north to the Han experimental farm for use in the upcoming farming season.
Photo by Vince Fedoroff
TILLING SUCCESS – Tom Bamford (far left) is seen Tuesday with the home-built tractor. It is headed north to the Han experimental farm for use in the upcoming farming season.
A home-built farm tractor was unveiled Tuesday during this week’s annual conference to promote advancement of agriculture in the territory.
A home-built farm tractor was unveiled Tuesday during this week’s annual conference to promote advancement of agriculture in the territory.
The tractor was put together by a team of locals using designs available through Open Source Ecology, which provides free blue prints and material lists for use by the general public rather than commercializing and profiting from product initiatives.
Team member Tom Bamford told the conference audience the Bobcat-like machine cost about $15,000 to build.
It will be loaned out for the upcoming season to the Han experimental farm outside Dawson City. It will be put to work there so operators can get a feel for the tractor and report back with any recommended changes, he said.
Bamford said there are several advantages of using the Open Source network for accessing machinery and other products.
Open Source was created to share ideas and information and provide affordable options by avoiding corporate commercialization, he explained.
Bamford pointed out the Open Source Ecology centre in Missouri and its Global Village Construction Set has a line of 40 machines, including the LifeTrac design Bamford and company used to build their tractor.
As part of his presentation, one slide showed the late Mr. Spock – Leonard Nemoy – in a pensive pose beside the quote: “The miracle is this – the more we share, the more we have.”
The LifeTrac tractor is not only meant to be affordable. It’s basic in design so that repairs are not complicated or tricky, but are straightforward and can be done by the owner or operator, he said.
“There is not to much that could go wrong, but if something did go wrong, I could replace one of the those motors in about an hour,” he said of the four hydraulic units driven by a 27-horsepower gas engine.
“I do not know if you could do that with your car these days.”
In an interview afterwards, Bamford said he is hopeful the home-built tractor unit is a solution that is applicable in the North not just for farming, but quite possibly for smaller placer mining operations.
Raised in Faro, he knows mom and pop placer operations that have had their season gutted or foiled altogether by costly and sophisticated equipment failures.
Yukon College and Yukon Agricultural Association commissioned Bamford and Logan Sherk and their company, Arctic Automate, to build the tractor, which has now been named NorTrackTor.
“What they were really wanting to do is see how the price points compare and to see how it works with people in remote locations like the Han experimental farm and similar farms, and how it helps, without tractor break downs,” he said. “They are trying to encourage less of a barrier to commercial farming.”
It cost $15,000 in materials, took approximately 160 hours of labour to build and weighs an estimated 3,600 pounds. The crew began working on it about a month ago, and literally finished the night before the unveiling.
It does not have a standard three-point hitch used on farm tractors, nor does it have a power take-off attachment, but it is fitted with an extra hydraulic unit that can be used to power a variety of farm implements.
The bucket is capable of lifting a 1,000-pound bale of hay.
Bamford said they intend to build a rotor tiller – design from Open Source Ecology – that can be used with the tractor to assist the Han experimental farm with field preparation.
But before they do, they’ll be talking to representatives of the farm to determine if they want to be involved in the construction of the tiller, and to what extent.
Most parts for the tractor were ordered from down south and were shipped in, though the steel was provided by Ajax Steel, a local supplier.
Bamford said they wanted to establish a true price comparison with the southern market using an established chain of supply.
It’s likely buying parts that are available locally will result in noticeable savings, he said.
Bamford said in the scheme of things, $15,000 is relatively affordable, considering a tractor on the open market with the same capabilities and durability – but much more sophisticated – could run $40,000.
The tractor could easily be built through the off-season by a farmer or placer miner who had the right tools and a $400 welder, he said.
Learning how to do the welding required, Bamford added, would take somebody half a day.
Sherk, who also serves as the facilities manager for YuKonstruct, the territory’s first makerspace, told the crowd gathered for the unveiling that with three other people who knew how to drill holes and operate a saw, he could build the machine in three days.
“I just hope it is a solution that is applicable here,” Bamford said, noting the North has an ample supply of do-it-yourselfers.
The Han experimental farm is a joint initiative between the Tr’ondek Hwech’in of Dawson City and Yukon College.
The intent is to re-establish crop farming a piece of Tr’ondek Hwech’in settlement land that was known in the Gold Rush days as the Strachan Farm.
In order to encourage thoughtful and responsible discussion, website comments will not be visible until a moderator approves them. Please add comments judiciously and refrain from maligning any individual or institution. Read about our user comment and privacy policies.
Your name and email address are required before your comment is posted. Otherwise, your comment will not be posted.
Comments (1)
Up 11 Down 14
Just Say'in on Mar 27, 2015 at 9:25 pm
Or you could just buy a machine that is used and has a supply network and parts availability. I very much doubt that this "home built" unit passes safety standards. The Roll Over Protection or "ROPS" standards are very specific for this type of equipment and requires testing and certification. There is a reason that the parts are harder to change on a proper machine. You have to have heavy armour everywhere on the machine to protect the occupant from trees or rocks and debris from crushing the driver. I think this is a joke and not well thought out. Must be a big Government grant involved.